在企業資訊化應用領域中,”如何協助製造業提升整體競爭力”一直是產業界與資訊業界共同努力追求的重大目標,但是仔細分析大多數製造業的資訊化成果,歷經MRP、MRPII、ERP等各階段,真的能達到資訊化的理想目標從此高枕無憂嗎?可能很多人得不到滿意的答案。我們先下列的表格內容來觀察各階段資訊系統的演變與差異。
|
系統訴求重點 |
無法滿足製造業功能需求的項目 |
MRP |
每週一次依出貨日逆向安排生產計劃,以此算出材料需求之後在最佳時點購入適當數量的材料。 |
1.未考慮材料以外的因素,所以生產計劃與實務脫節。
2.不適合少量多樣多變化的生產模式。 |
MRPII |
改善MRP的缺失,系統完整考慮生產相關所有因素,排出正確可行的生產及採購計劃。 |
架構觀念正確但是資訊系統實際功能無法配合。 |
ERP |
以財務為基礎整合所有作業流程,依據表單過帳更新相關帳目結餘數,讓所有資訊即時同步並透明化,特別著重財務面管理功能。
|
1.仍以MRP為主軸,無法提供符合實務的生管相關功能。
2.不具備模擬比較不同生產計劃優缺點的功能,無法提升產銷協調效率。
3.無法在接單前排出正確的可承諾交期ATP
( Available To
Promise )。 |
※
物料需求計劃MRP
( Material Requirement Planning
)
※
在90年代以前;全球整體經濟環境各項演變節拍較為緩慢,因為規格化大量生產的觀念主導經濟發展趨勢,大多數企業的整體營運策略普遍採用計劃性大量生產壓低成本,必要時於銷售末期配合促銷作業出清庫存,所以製造業所接到的訂單通常是少數的品項規格長期大量生產。當時尚未普遍應用的資訊系統規劃為每週執行一次MRP運算,依據客戶要求的出貨時程及數量參考預估的生產所需時間之後,逆向推算應該上線生產的時間安排出生產計劃,然後以生產計劃展開算出需要投入材料的日期與數量。
此階段的資訊系統概念強調以投入材料為主要管理重點,只要能解決材料問題,一定有足夠的產能搭配進行生產,而且因為訂單狀況通常是穩定不變並且有足夠的生產作業時間,所以每週進行一次檢討並且小幅調整即可正常運作。這種有限材料無限產能的基本概念在接單後有充分時間可供生產作業的環境下,可以發揮一定程度的效益。對於資訊業界來說,這樣的運作架構也比較容易進行系統的開發與維護。
※
製造資源計劃MRPII
( Manufacture Resources Planning
)
※
進入90年代之後,許多產業基於成本與應變能力的因素將製造作業移到亞洲地區,台商製造業的應變能力也陸續在國際舞台展露出驚人的競爭力,在此同時供應鏈的觀念也逐步成型,企業競爭模式由過去的單打獨鬥逐漸演變成為不同供應鏈之間的競爭。與80年代相比較,此階段的企業運作逐漸放棄計劃性生產制度,改為依據市場需求狀況下訂單生產後交貨以避免成品庫存損失侵蝕獲利,於是製造業越來越難接到長期穩定生產的訂單,訂單的平均數量日漸降低,可容許製造業進行生產的時間也逐步縮短,製造業發現必須更有效率的進行生產過程中的各項作業,才有可能降低庫存風險並且爭取更多訂單。
仔細檢視製造業的實際運作環境中,材料與產能必須互相搭配同時到位,才能以最高的效率完成生產並且將成本控制在一個合理可接受的範圍之內,原先所奉為圭臬的MRP架構在此遇到挑戰,僅規劃材料而不考慮其他因素顯然不足,所以此階段中開始出現了製造資源計劃MRPII的觀念,強調除了供應足量的材料之外還要考慮購料成本與必要的製造成本,完整規劃製造過程中所需的各項資源,才能有效提升製造業競爭力,此時觸及如何有效運用產能降低直接人工與製造費用的問題。整體來說;MRPII是一個正確的觀念,但是當時的資訊技術卻無法配合提供所需的各項運算功能,於是它變成一個難以達成的理想而逐步被人淡忘,時至今日已很少人談及此事。
※
企業資源規劃ERP
( Enterprise Resources Planning )
※
繼MRPII之後出現了企業資源規劃
ERP這個名詞,搭上Y2K的列車,產業界迅速進行各項系統升級作業,紛紛將不理想的MRP與失敗的MRPII更換為”以財務為基礎全面整合各項作業流程”的資訊系統,許多人認為若不執行ERP將會落伍遭受淘汰而忘了仔細分析ERP系統實際功能是否合於自身的需求。一窩蜂趕流行追求新名詞的結果是;許多企業執行了號稱ERP但實際上卻不完整的系統,更有一些製造業執行了功能完整的大型ERP系統,但是卻發現其中的生管模組與MRP模組功能不彰,所以雖然有ERP作為整體運作與管理的基礎,但是因為系統中的功能與生產實務脫節無法發揮效益,所以要靠人工配合Excel進行生產管理,使得當初決定更換ERP系統時期望增加競爭力的期望與現實成果發生一定程度的落差。
既然ERP系統中有生產管理模組與MRP模組,為什麼無法發揮預期的效益?主因在於隨著網路的發展全球經濟發生了巨大的變化,各項資訊透明而且強調快速與個人化,所有的製造業均面臨少量多樣短交期的挑戰,客戶普遍要求製造業在接單前快速回覆交期,並且要能信守承諾才有機會爭取更多訂單。在此同時;由於各項技術的演進速度加快,各種新材料不斷推陳出新的結果導致庫存風險大幅攀升,資材控管與採購作業面臨更大的難題,製造業的運作顯得更為複雜。
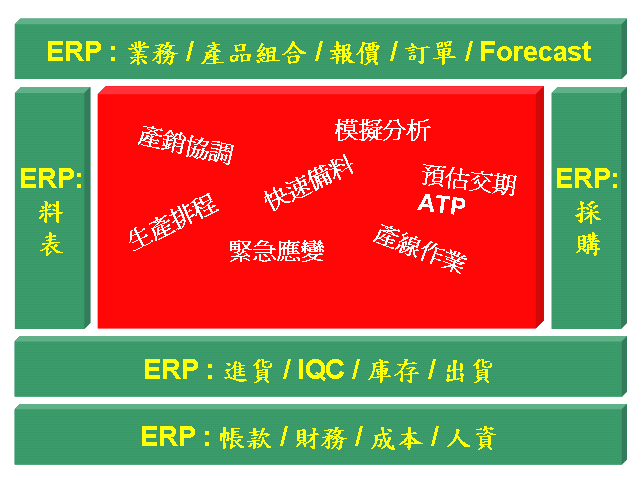
※
先進規劃排程系統APS
( Advanced Planning & Scheduling )
※
為了彌補現實與理想的差距,製造業所應用的資訊系統中出現了APS這個名詞,我們從上圖的內容可以發現,以製造業的運作複雜度為依據來分析,ERP系統提供了周邊各項以表單為基礎的功能,但是由生產作業所衍生的各種複雜問題,卻是大多數ERP系統避之唯恐不及的,所以執行ERP之後當然不能讓製造業真的脫胎換骨,還必須要以APS解決問題的核心。從系統主要功能面來判斷,APS與ERP之間的關係是互相搭配運作而不是互相取代。
下圖顯示出ERP與APS另一項重要的基本差異:圖中下方的箭頭符號顯示出時間軸方向,ERP系統主要功能為依據已確認的表單結算出各項帳目數據供各使用者查詢,以便進行有效的合理的運作,基本上ERP是處理時間軸當中過去的時段內所有確定生效過帳後不再變動的資訊,將結果在現在的時點呈現出來備查。

APS則與ERP不同;它是依據現有的資訊計算出未來的狀況,通常以目前應進行生產的工作項目為基礎,參考未來可以供應的各項相關資訊(廠內及委外的各項產能/材料及半成品供應狀況/設備與模具的使用率…)快速運算預測出與生產相關的資訊,讓使用者可以事先預知未來的整體生產與出貨狀況,若有必要可以直接查詢可能發生的問題及相關資訊,預先安排因應對策提前協調解決問題,讓企業在最低風險的情況下以最高效率運作,從而降低成本提高客戶滿意度。所以在圖二的時間軸上面可以看出APS專門用來處理從現在到未來的相關資訊。
整體來說;APS分為規劃與排程兩大部分,前者依據需求(訂單、預估計劃、樣品、重工、接單前預估交期…)規劃出適當的生產數量及前後製程生產作業關係,後者則依據規劃所得資訊參考產線可用用的產能狀況、材料供應狀況、各項設備與模具的使用率等相關因素,安排最佳生產計劃,以最有利的條件及時生產出適當產品滿足各項出貨需求。
若是遇到相關條件大幅度變動,例如:緊急插入新單或抽換訂單品項數量,或是產線發生狀況某段時間無法生產,或是材料供應發生問題導致部分品項無法進行生產,則需要進行相關部門的協調尋求最可行的應變方案,此時需要在APS之中使用多重模擬功能,每個模擬區域中的應變方案採取不同的加班或調班或委外加工的方式進行排程,然後在不同模擬區之間交互比較分析找出最佳方案做為正式執行作業的依據,所以在APS當中絕對需要多重模擬排程功能,才能在重要時可發揮應有的效益。
另外;在某些情況下客戶會預先詢問可承諾的交貨日期然後才決定是否正式下單,此時需要在APS中執行承諾交期ATP
( Available To Promise )功能,依據尚未確定的訂單資料產生ATP製令在系統中進行規劃與排程得知交期,並且評估對生產作業及既有訂單交期的影響程度。若確定接入訂單則將前述ATP製令轉為正式製令依計劃進行生產,如果最後結果並未接到訂單則將前述ATP製令刪除,讓系統重新依據最新狀況進行排程。
以上簡要概述系統功能差異及APS的主要用途,後續將另行安排深入介紹APS系統架構與功能。 |