阿基米德說:「給我一個支點,我可以舉起整個地球。」當然最後他不可能把地球舉起來,因為他跟本沒有可用的資源,或許我們應該更清楚的說「沒有資源的計劃是無法實現」。
製造資源是生產作業的要素之一,它可以靈活的移轉配置在某一條產線(或機台)上執行作業,但它也會忽然間讓你捉襟見肘應變不及,就算是萬事俱備只欠東風也是徒呼負負無可奈何
。所以製造資源的使用如果不能取得充份的支援,就需要經過合理的規劃安排,才不會成為生產管理中追求高效率的絆腳石。
簡單來說,製造資源泛指所有在生產過程中可能使用的人力(作業員/技術員…)或設備(儀器/模具/治具…);它是生產排程的要素之一,當然也說明了它的重要性,我們已經在「製造資源對排程的影響」文中,做了基本概念的說明;我們繼續以情境模擬的方法,屒示說明神燈在有限製造資源下的排程解決方案。
一、製造資源的設定
A.BA製造資源主檔
在「BA製造資源主檔」程式我們建立製造資源基本資料明細,對排程有影響性的資源(有限條件),我們也設定為限制型的資源,如下圖程式畫面紅色標示的項目。
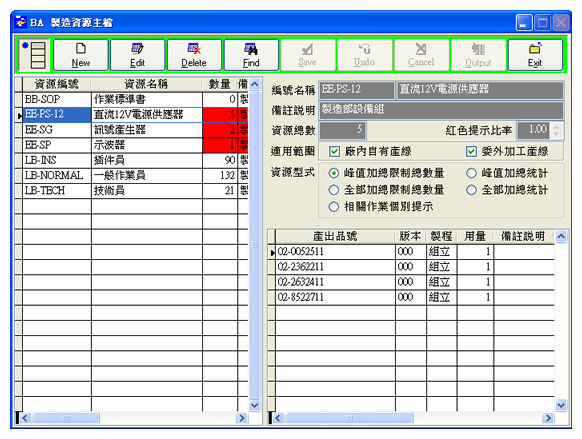
限制型資源的設定:
»峰值加總限制總數量:代表同一條產線在同一個小時之內進行多張製令時(換線或是多張小製令),以其中的最大使用數量為計算依據。
»全部加總限制總數量:代表同一條產線在同一個小時之內進行多張製令時(換線或是多張小製令),將所有使用數量全部加總作為計算依據。
製造資源的適用範圍:
製造資源在排程計劃中受到總量限制的控管,所以計算(使用)的範圍也有所區分,若資源僅使用在廠內產線,則設定為「廠內自有產線」,如果資源必需跟隨製品移轉到委外產線而與廠內線共用,則總量的計算也需包含「委外加工產線」的用量。
B.BB製造資源標準用量
在「BB製品的標準用量」程式內設定資源的標準用量,如下圖程式畫面所示,每一個產製品號可設定資源品量需求,做為生產及排程條件。
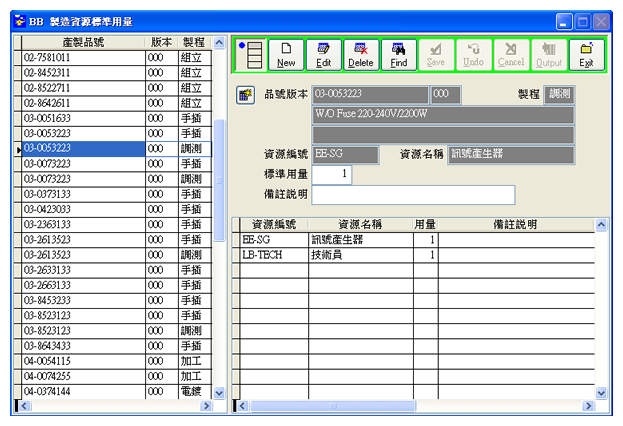
二、製令生產所需的製造資源
當製品產生製令後會將資源標準用量做為排程的條件之一,製令基本資料的內容也會列舉資源明細,如下圖EE程式畫面「製造資源」頁框所示。
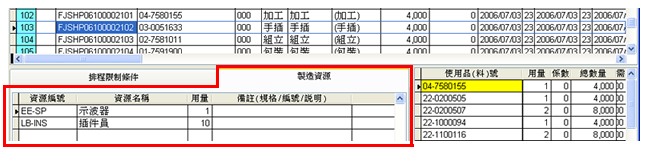
三、生產排程及應變措施
A.資源不足的排程限制
製造資源為排程中限制性的條件,如果發現資源總量不足時就會採取遞延尋求可行的排程方案,如下圖排程畫面圖示。
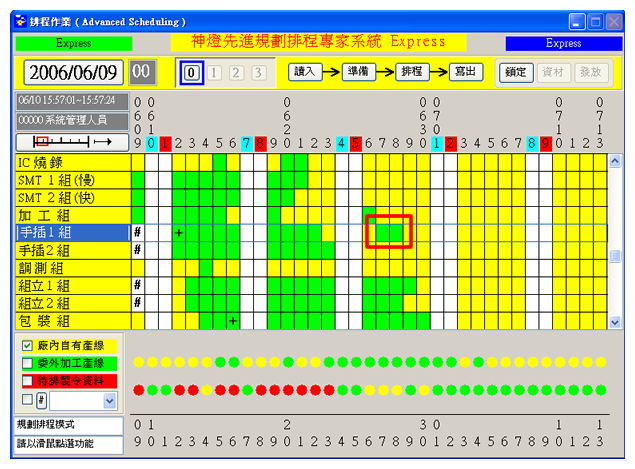
受到限制的製令在「EE子製令排程總表」程式內「排程限制條件」的頁框內,也會列出資源不足及受限制時間明細的提示,如下圖程式畫面所示。 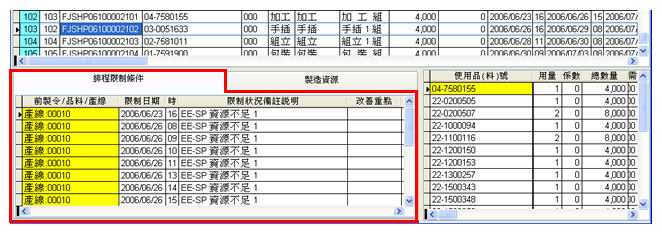
在沒有資源的情況下是無法執行生產的,所以經過排程遞延後,產生的是一個可行的生產計劃,同時出現限制資訊提示。 B.受資源限制的應變措施 生產排程最難以程式化的原因是因為在現場實務上充滿了各種可能性,我們設定了排程條件,但常常發現它不是絕對的條件,山不轉還有路轉總是考驗著系統的應變能力,所以系統提出的解決方案,必需要能符合實務應變的需求。 1)製造資源受到限制時可能的應變措施: »更換排程優先順序:如果排程優先順序可以更變,則更換製令排程優先順序,使不急需的製令遞延而不影響主要生產目標的達成。 »轉發委外生產:如果製品可委外生產且不佔用資源,則可依系統提供的限制資訊,選擇適當的製令排入委外生產線也可以快速解決限制問題。 »修改可上線日期:實務的解決方案,也許更為多樣化,如另外提出資源的替代方案、資源器材的短期租用支援...等等;在程式的處理上,只要取消資源的限制或同時設定上線限制的日期,即可順利完成符合實際狀況的生產計劃。 2)我們以畫面展示修改可上線日期的解決方案:
假設在此例中我們以短期租借示波器的方式突破限制,經洽詢得知最早可借入的日期為2006/06/23,表示此一製令雖然可以不受示波器的數量限制,但是不可在2006/06/23之前上線,製令勾選「無限資源」並設定「上線限制」日期後的排程結果,如下圖程式畫面如示: 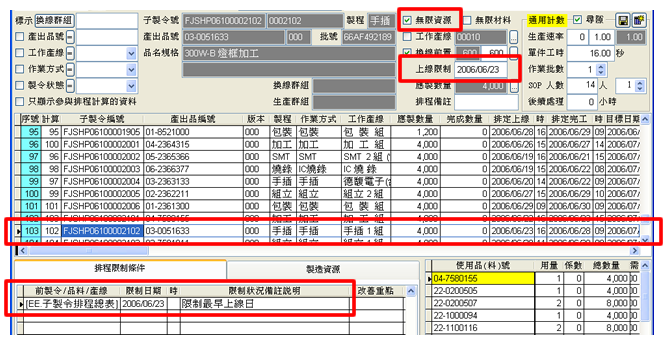
(上圖製令依「上線限制」排入上線時間,在「排程限制條件」頁框內也提示限制最早可上線日) 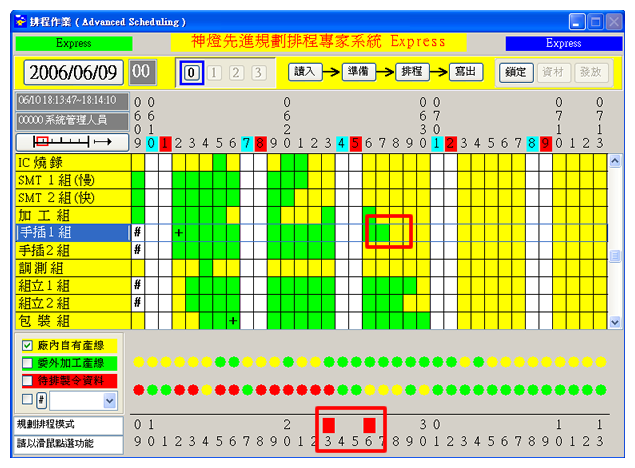
(上圖原本被遞延的排程圖示也已經變更,在程式畫面下方出現二個紅色方塊表示資源的使用量已經超過警示量。) C.限制型製造資源使用的提示 限制型資源在排程的使用上,原則上必需符合有足夠的可用量才可能排入排程;但如果在應變調整中取消資源的限制,那在數據的計算上可能會出現超用的情形,這時系統會出現紅色的警示方塊,提示製造資源的超用狀況。 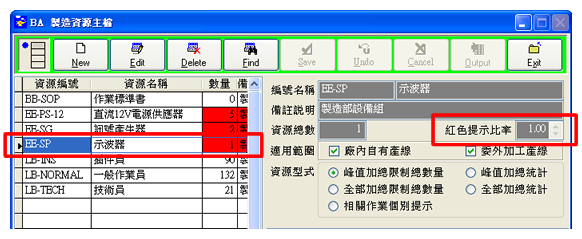
從上圖BA程式畫面看設定EE-SP示波器的資源數量為1,紅色提示比率為1(即符100%以上)。
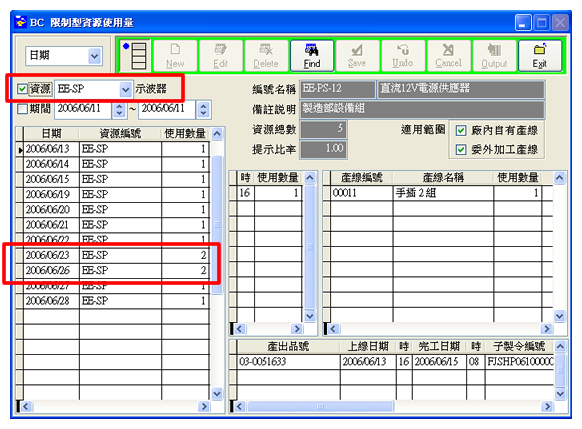
完成排程後實際使用明細在2006/06/23及26二天都超出提示比率的設定值
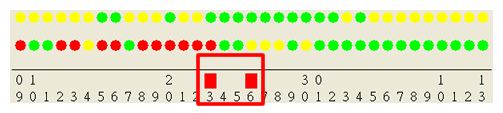
上圖在排程作業畫面(Advanced
Scheduling)的程式畫面下方就會出現紅色方塊的提示;當然如果資源總量可以跟著修改,則不會有紅色提示出現。
製造資源、產能工時及資材數據我們稱為排程運算的三大要素,這些要素在生產作業過程中,如果沒有充份的支援或供給,計劃與現場實務也只是各吹各的調,所以
為了要產生一份可以發揮最高效率的生產計劃,不得不重視排程運算過程是否已經合理考慮了所有生產排程要素。
|