隨著市場快速的變化與競爭,製造廠的競爭趨向於速度、成本與品質的競賽,這使得製造廠的管理又更微觀於以往;以前或許緊盯著訂單、庫存就可以掌握獲利;但現在已經走向微利的競爭,生產成本也必需經過嚴格的控管才能
強化競爭力;在市場去庫存化的大趨勢,客戶適量適時的下單,製造廠藉著增加產品組合來提高接單率,所以多樣化的接單也是時勢所趨;整體而言受到市場因勢利導「多種少量,短交期的生產模式」已經變成製造廠所必需要面對的挑戰。
「多種少量,短交期」的生產模式,從製造的角度而言,影響最大的,不外乎是「生產效率」的發揮,產線為了應付「多種少量,短交期」的出貨需求,必需不斷的「換線」生產不同品項來應付出貨需求,「換線」作業必然影響生產時間,不管快慢長短,都影響到產出效能;所以「換線工時」在機械業或金屬加工業的生產管理上,一直是一個被重視的問題,尤其是複雜或是精密的機台一次的set-up往往要花上數個小時的時間,暫且不去探討其中技術性的問題,我們用不同的思維方式也可以有效縮短換線所發生的遞延時間,這樣的觀念我們利用生產排程的解決方案,也可以達到將換線工時縮到最小化的要求。
神燈先進規劃排程專家系統開發了「最少損失」的排程原則,這個觀念源自於生產排程計劃必需要能尋求生產效益的最大化,若從尋求產能充分發揮的觀點上,「最少損失」的排程原則不外乎是最好的選擇,神燈系統能夠以最少換線工時的條件來做排程,減低反覆而不適當的換線浪費,增加實際的生產稼動時間,提昇了「多種少量,短交期」生產模式中的生產效益。
由於機械或是金屬加工產業,所使用的機台如車床、銑床、磨床..等,常常需要多個模治具或工具的適當組合搭配才能夠驅動生產,基於這樣的生產特性,神燈系統將製品的模治具分別設定參數做為排程的條件,將相同或是最少更換模治具的製令歸納排程,來達成最少換線損失的生產計劃,我們以車床的生產排程來說明:
神燈先進規劃排程專家系統在排程原則的規劃有二種:
A.最早完工:在考慮產能、製造資源、材料及其他限制條件下,以最早可完成工作的時間,依序排入製令上線。
B.最少損失:在考慮產能、製造資源、材料及其它限制條件下,以最少換線(模)前置準備工時條件,依序排入製令上線。
(下圖為神燈系統在EB程式設定「排程原則」)
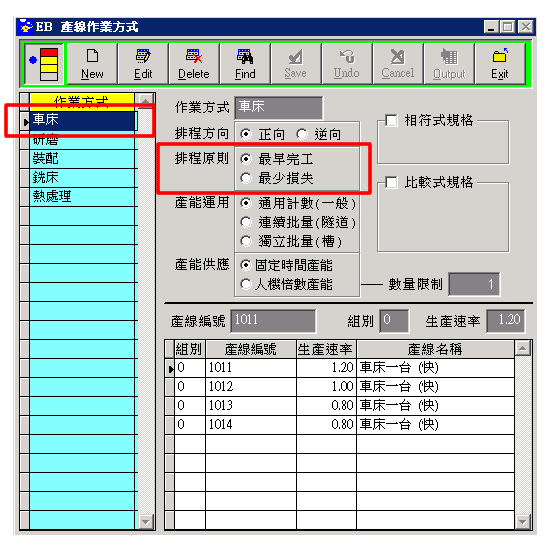
我們以神燈系統實際做第一個模擬,使用「最早完工」的原則下執行排程並完成生產計劃,我們計算車床(車床一台至四台)產能需求
在4/13~5/1之間總共需要「56」個工作天才能完成所有的製令,如下圖所示(每一個綠色方塊為一天的產能需求)。
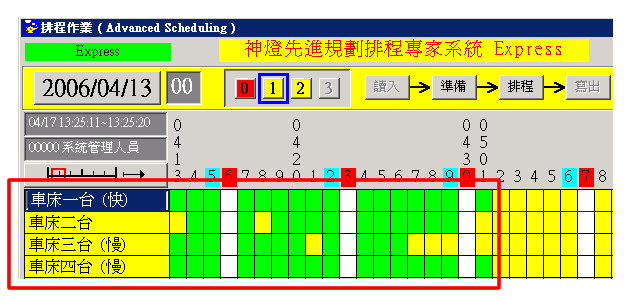
我們以神燈系統實際做第二個模擬,使用「最少損失」的原則下執行排程並完成生產計劃,我們計算車床(車床一台至四台)產能需求
在4/13~4/29之間總共需要「54」個工作天,就能完成所有的製令,如下圖所示(每一個綠色方塊為一天的產能需求)。 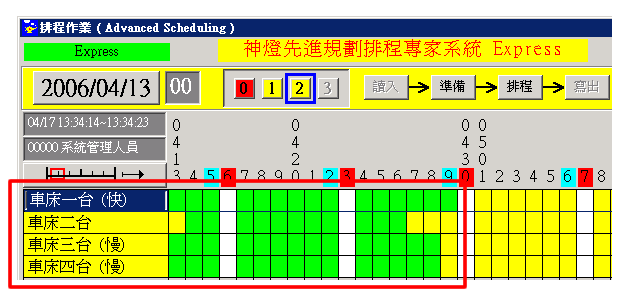
由上述二種排程原則的比較,可以發現同樣的生產內容與條件,但因使用不同的排程原則,產能的需求相差了「2」天,這
兩天的差異就是換線的時間差;如果以「最早完工」的原則來排程,則因追求最早完工的效益而損失了兩天的產能,反之若以「最少損失」的原則排程,就可以節省
兩天的產能,所以對於換線內容複雜前置時間長的機台,善用「最少損失」的排程原則,將能發揮最大的產能效益。
神燈系統對於多段式換線前置的規劃 非常靈活而容易入手的,我們可分為區段規劃及製品設定二部份,以下我們來說明多段式的規劃及設定原則。
區段規劃: 
神燈系統在多段式的換線前置規劃了五段的參數運用空間,這五段也可分為獨立區段及階層區段二種,這二種特性不同,完全依需要規劃設定;可以只取其一種或是二種並存,但總共以五段區分為原則,雖是五段但因可以多碼設定分類,可應用空間相廣大。
獨立區段:各項生產作業所需的工具依需求各自更換及計算換線工時,其它
工具則不受影響,在上圖的例子中如刀具、砂輪及鑽頭類等是(藍色框內者),譬如只更換砂輪則只計算砂輸的換線工時,其餘
工具可以沿用則不發生換線工時。
階層區段:只要這類的模治具更換,就必需將後續各階層的所有模治具一起更換,如上圖所列舉的夾頭、模座等是(紅色框內者),
如果換現時必須更換夾頭,則包含模座必需跟著計算更換所需的時間,換線工時也以實際的更換內容所需時間加總計算。
製品參數設定:
對製品生產所必需使用的模治具
及工具,也設定為換線群組及代碼,在每一段模治具及工具物件均設定其所需要的換模時間,如此在神燈系統即可依「最少損失」的原則,完成最少換線(最少損失)時間的排程。
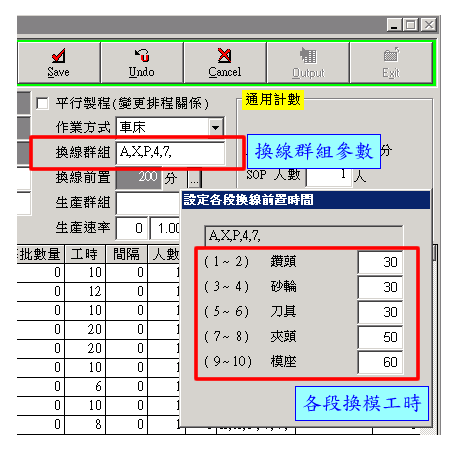
以上是針對機械業或是金屬加工業普遍使用的車床機台舉例介紹,主要說明機台設備在「換線」內容複雜且前置工時長的情況之下,以「最少損失」的排程原則,爭取最少產能損失所產生的排程效益;如果換個觀點來看,生產交期短,而換線損失有限的情況下,採用「最早完工」的排程原則,則對訂單交期的掌握也將有最佳化的表現,至於使用者如何運用這二種不同的排程原則,必需依實際生產狀況的
需求靈活設定,才能發揮最大的排程效益。
|